智啟未來 中國煤炭科工解鎖無人化採煤新密碼

在榆家梁煤礦調度中心的大屏幕上,43207智能工作面的數據實時跳動。兩名監控員按下綠色按鈕,智能工作面裝備隨即全自動運行,採煤機自主規劃截割路徑,液壓支架自適應調整支護姿態,刮板輸送機精准協同運煤,煤炭順著皮帶源源不斷地輸送到地面上。
這是中國煤炭科工集團所屬天瑪智控打造的“0+2+2”無人化採煤新模式,在這個工作面上,生產期間採場無人作業,順槽2人監護,地面2人遠程監控,生產效率提升16.7%。這個曾經每班需要11人值守的工作面,如今實現了“地面規劃採煤、裝備自動執行、面內無人作業”的常態化運行。
榆家梁煤礦43207工作面地面控制中心割煤實景
破局“卡脖子” 實現從“跟跑”到“領跑”
改革開放以來,我國煤炭產量逐年提升,對煤機裝備的需求越來越大,液壓支架等大型煤機裝備已基本實現國產化,但是控制液壓支架的核心技術裝備——電液控制系統長期被國外壟斷。
電液控制系統引進初期,國外對我國實行技術封鎖,而且設備價格昂貴,嚴重阻礙了煤炭行業的健康發展。2001年7月,為了推動我國煤礦開採技術向自動化方向發展,中國煤炭科工集團出資成立天瑪智控,用中國技術守護礦工安全。
“我們白手起家,面臨著缺乏團隊、技術封鎖等困難,產品從樣機到車間再到現場,歷經上千個日夜的反復修改與驗証。”談起首套SAC型液壓支架電液控制系統的研發,當年的主要研發人員仍然心潮澎湃。研發團隊克服測試標准缺失、測試儀器不全等困難,在不斷摸索中積累經驗,在劈波斬浪中砥礪前行,在一次次的失敗中再接再厲。“研發的日子雖然枯燥,但每一點小小的進步都讓我興奮不已。”
2008年12月,依托“十一五”國家重點技術創新項目支持,我國首套自主知識產權SAC型液壓支架電液控制系統橫空出世,攻克了電液轉換技術難題,並在國家能源集團寧夏煤業石溝驛煤礦投入使用,一舉打破國外多年的技術封鎖,實現了電液控制系統的“中國化”。
十年磨一劍。天瑪智控持續攀登技術高峰:2014年,SAM型綜採自動化控制系統在陝煤集團黃陵礦業1001工作面應用,首次實現了採煤機記憶截割、液壓支架自動跟機作業、綜採運輸設備集中自動化控制,開創了地面一鍵啟停、遠程割煤,採煤工作面支架支護區域“有人巡視,無人操作”的可視化遠程干預智能開採生產模式應用的先河,引領了我國煤炭開採從綜合機械化開採向無人化智能開採的轉變。2017年,天瑪智控又成功研制出了630L/min、40MPa高端乳化液泵站,打破了國外產品在高端泵站領域的技術壟斷。
目前,天瑪智控已經形成了SAM、SAC、SAP三大核心產品,通過“大腦—神經—心臟”的有機協同,構建起煤礦智能化開採的閉環控制體系,在打破國外技術、產品壟斷的同時,核心產品技術、性能、質量、可靠性等均達到了國際領先地位。
“十三五”期間,國家能源革命戰略的推進,使煤礦智能化轉型成為行業發展的必然選擇。中國工程院院士、中國煤炭科工集團首席科學家、天瑪智控科技委主任王國法介紹:“我們以‘智能開採控制技術及裝備’等核心課題為抓手,攻關煤層精准探測、人工智能、大數據、工業互聯網等技術,探索‘透明工作面’的智能無人化開採理論及技術實踐,形成了採煤裝備自主感知、自主決策、自主控制的智能化自適應採煤模式。”
現在,主要技術成果正在全國煤炭企業500多個工作面上應用,成為中國煤科智能制造走向世界的閃亮名片。
科技攻堅,挺進無人化採煤“深水區”
我國煤礦智能化開採技術已經處於國際領先水平,科技創新也進入了深水區,亟需通過自身努力,取得更多原創性、突破性的技術成果。
2020年2月,國家八部門聯合印發的《關於加快煤礦智能化發展的指導意見》提出,到2025年,綜採工作面內達到少人、無人操作。天瑪智控以提升煤礦工人安全感與幸福感、實現煤礦轉型升級和高質量發展為使命,發布“無人化採煤控制系統研發與應用”攻關項目,專題攻關無人化智能開採控制技術難題。
2021年盛夏,天瑪智控面向行業廣發“英雄帖”,廣邀英才攻克無人化採煤難題。明知山有虎,偏向虎山行。王峰、劉清2位揭榜人從7支揭榜團隊中脫穎而出,帶領榆家梁、黃陵2個團隊以國家能源集團榆家梁煤礦和陝煤集團黃陵一號煤礦作為示范項目,通過“賽馬機制”攻關無人化智能開採項目。
在榆家梁、黃陵一號兩個煤礦,面對地面規劃截割極限位置自動返刀精度不足導致“割不透”的技術瓶頸,工程師團隊深入井下,反復測量嘗試,通過視頻監控系統捕捉關鍵標志物動態軌跡,深入分析數據規劃,成功突破設備空間定位補償、多傳感數據融合等核心技術,實現極限工況下的智能判定與連續多刀自主返刀作業。為獲取良好的現場數據,做好煤機位置計算和支架動作分析,團隊成員熬更守夜、廢寢忘食。疫情期間,團長和工程師們主動請纓,住進隔離帳篷,這樣可以及時進入礦區,推進工作進度。
“無人化採煤控制系統研發與應用”攻關項目
2022年寒冬,兩個示范礦井同時傳來捷報:榆家梁煤礦建成“0+2+2”的無人化採煤生產模式,生產效率提高16.67%﹔黃陵一礦建成“0+3”的無人化採煤生產模式,生產效率提高13.81%。兩項成果經鑒定,均達到國際領先水平,為我國無人化採煤提供了新樣板,標志著中國煤礦智能化開採正式邁入智能採煤新時代。
王國法院士表示,“十四五”期間,天瑪智控面向世界科技前沿、面向國家重大需求、面向人民生命健康,全力攻堅無人化智能開採控制技術,首創“地面規劃採煤、裝備自動執行、面內無人作業”新模式,真正做到採煤工作面支架區域內生產過程無人,確立了國內外煤炭開採的引領地位。
目前,該項成果已經在國家能源集團、陝煤集團、山東能源集團、四川嘉陽集團等多個企業所屬礦區推廣應用。
智能智造,鍛造智能開採“大國重器”
《中國智能制造2025》明確提出加快推動新一代信息技術與制造技術融合發展,把智能制造作為兩化深度融合的主攻方向,在重點領域試點建設智能工廠及數字化車間。
天瑪智控將智能工廠建設列入企業發展規劃,圍繞工廠建設、研發設計、生產作業、生產管理、運營管理等五大業務模塊,建成6套智能加工系統、8條柔性智能裝配生產線和多台(套)智能專機、1個大數據中心和20余套信息化系統,實現對廠區設備運行狀態與能源消耗情況的實時監控。
天瑪智控創新產業基地自動化產線
技術人員介紹:“在我們的智慧工廠,生產任務自動分解、生產計劃自動下達、生產過程自動執行、物料按需及時配送、數據智能分析、異常智能調度。每10分鐘下線一組電液控換向閥成品,每36小時裝備一個採煤工作面。從毛坯上線到成品下線,全流程實現自動化、智能化。”
“通過柔性生產線,實現了多品種產品柔性混線加工。以前需要3台機床、人工操作才能完成,現在一台智能設備就可以了,效率提升30%,還減少了90%的停機時間。”操作人員介紹。在裝配車間裡,通過AI、視覺識別、復雜調度等技術實現節約作業人員29名,效率提升36%,年產量可滿足全國半數以上煤礦用戶需求。
智造升級帶來質的飛躍。通過14個智能制造場景,實現了從研發到生產的全流程智能協同,關鍵設備聯網率達到100%,產品合格率達99.61%,產品研制周期縮短20.59%,全員勞動生產率提升20.65%。
展望未來,從智能採煤到多元化布局,中國煤炭科工所屬天瑪智控追求的不僅僅是企業的高質量發展,更關乎著整個煤炭行業在新時期的蝶變。在科技進步與環境保護並重的今天,天瑪智控正以創新驅動和戰略眼光,朝著智能化、數字化的未來不斷邁進。
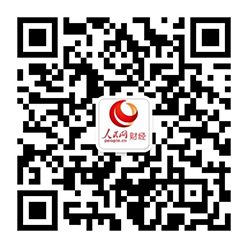
分享讓更多人看到
- 評論
- 關注