小設備破解“大飛機”精密打孔難題

大型運輸機、先進戰機等高端航空裝備內部結構十分緊湊、空間狹小。制造過程中,工作人員需要在復雜條件下加工近百萬個0.02毫米精度的連接孔,將成百上千萬個零部件精准連接起來。
如何在狹小空間實現復合材料、金屬強異質疊層結構的高質量鑽孔作業,是世界各國面臨的技術難題。長期以來,中國飛機制造的打孔環節多依靠純人工,而國外早已通過小型加工裝備實現了半自動、全自動化生產,產能是我國的5倍以上。
面對這一問題,受啄木鳥抓在樹干上打洞的啟發,大連理工大學一支年輕的學生團隊在中國科學院院士賈振元的指導下,變革加工模式,將固定在地面上的“包容式”加工,變為直接固定在零件上的“在體”加工。這種方法就像啄木鳥一樣,可靈巧且智能地完成“打洞”制孔。
要實現這個想法,需要解決復雜功能與高精度要求下小型化難、大波動負載下穩定控制難、千種工況精准快速識別難三大難題。團隊在相關企業駐廠數月,記錄分析加工現場特點,最終找到了突破口,創新提出空間降維式傳動方案、性能分級與全局最優設計方法。經過數萬次實驗探索,六代、數十台樣機迭代,一台A4紙大小的靈巧加工裝備誕生。相較傳統模式,該裝備的打孔方式讓加工能力大幅提升,加工效率達到人工的3倍以上,並且能適應原來人工無法適應的工況。但其加工質量還不夠穩定。
從“0到1”很難,但是從一到無窮大更難。在大量實驗的基礎上,團隊提出了基於末端反求的便攜式裝備精度與剛度分析方法,對影響裝備精度、剛度的關鍵零件進行優化,自主研發力、扭、振三源信息感知模塊,發明雙驅動同步預測控制算法,面對波動幅值較大的工況也可以穩定控制,使誤差降低至2%,遠低於國外誤差數值。同時,團隊建立了10萬以上的高質量數據集,首創火眼金睛“透視”算法,使裝備能夠在0.1秒內識別材料加工狀態,並切換至最優參數,加工成品率達100%。
“以往使用的機床價格昂貴、設計復雜、技術門檻高。我們的設備操作門檻低,工人師傅隻需對准位置、一鍵啟動即可自動加工。單孔耗時由5分鐘減至0.5分鐘,並將加工精度提升1級。”團隊成員、機械工程學院研究生常宇豪介紹。
“我們的控制芯片、電路板,包括前期採用的國外驅動器,現在都已實現自主設計。”團隊成員、控制學院研究生朱煬爽說。目前,團隊發明的系列智能化靈巧加工裝備已成功應用於航空裝備制造,加工能力達到國際先進水平,未來還可推廣到航天、船舶、車輛、能源等領域的高端裝備制造。
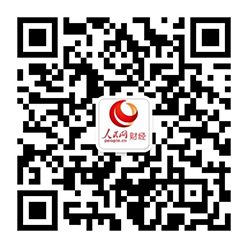
分享讓更多人看到
- 評論
- 關注